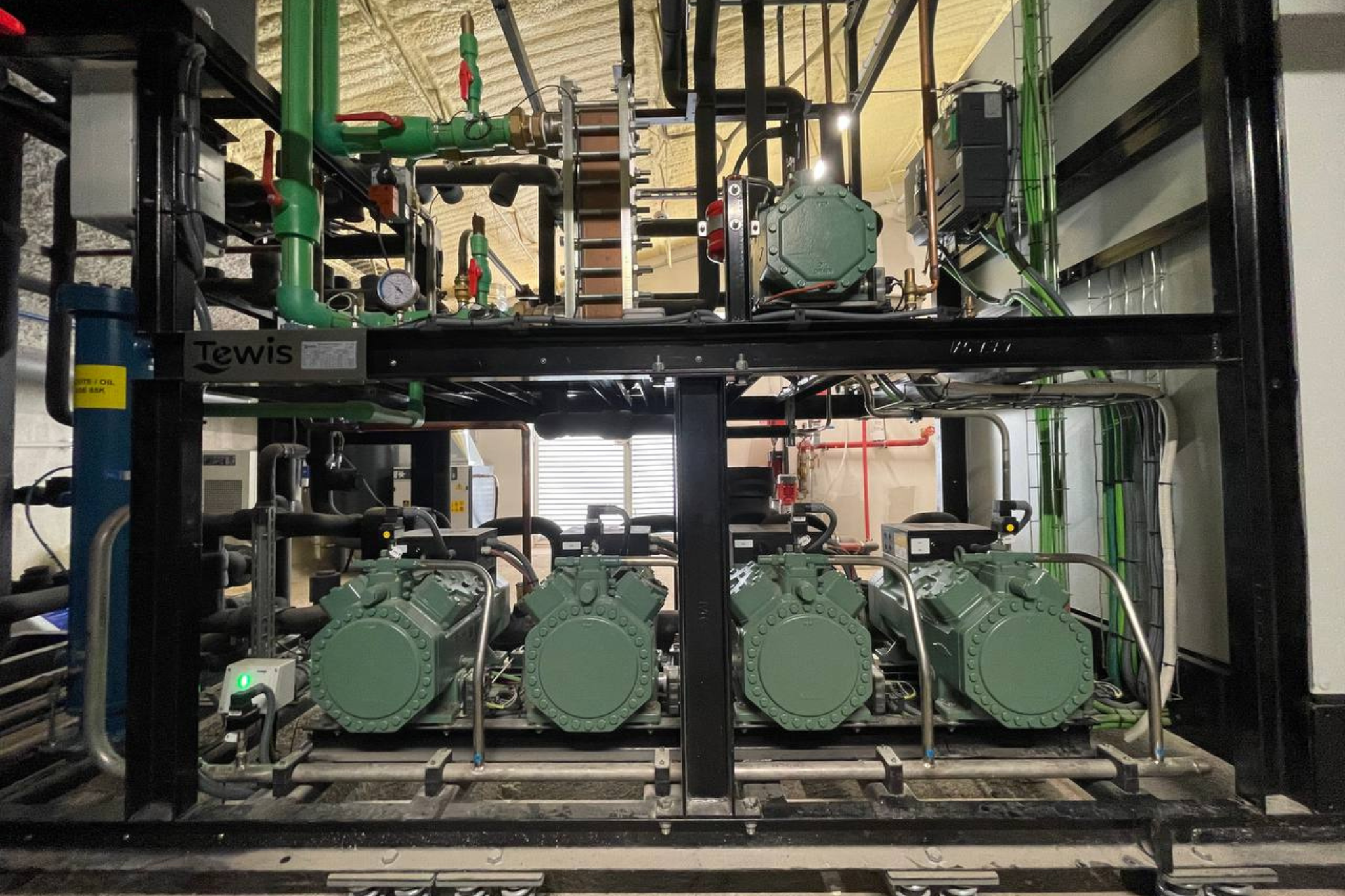
04 Apr CO2 REFRIGERATION: THE EFFICIENT AND SUSTAINABLE SOLUTION FOR COLD ROOMS
In the highly competitive industrial refrigeration sector, success demands more than experience — it requires energy efficiency, environmental responsibility, and technological adaptability. In this context, CO₂ refrigeration in transcritical cycle has emerged as one of the most efficient alternatives to conventional systems based on synthetic refrigerants.
Increasingly adopted by supermarkets, logistics centres, and food industry facilities, this technology not only meets the most stringent environmental regulations but also delivers tangible operational advantages. Why are so many companies choosing transcritical CO₂ systems for their cold rooms? Here’s a detailed explanation.
What is Transcritical CO₂ Refrigeration?
CO₂-based refrigeration systems use carbon dioxide (R-744) as a natural refrigerant. Under certain ambient conditions — typically at higher temperatures — the refrigerant operates above its critical point (31 °C and 73 bar), entering a transcritical regime. In this state, CO₂ does not condense as a liquid like traditional systems but instead cools down as a supercritical fluid.
These systems require specific components such as gas coolers, electronic expansion valves, and advanced control systems capable of precisely managing pressure and temperature fluctuations. While technically more complex, they offer highly efficient performance when properly designed and installed.
Technical Advantages for Industrial Refrigeration
1. High Energy Efficiency
Transcritical CO₂ refrigeration systems are particularly efficient in cooler or temperate climates. Thanks to technological advancements like parallel compression, vapour injection, and ejectors, these systems often outperform traditional HFC-based alternatives.
2. Superior Performance in Cold Rooms
In facilities requiring multiple temperature zones — such as large cold rooms or distribution centres — CO₂ allows for better heat recovery and precise temperature control. Its high volumetric efficiency also ensures more effective heat transfer with lower pressure drops.
3. Reliability and Maintainability
Despite operating at higher pressures, modern systems are engineered for safety and long-term reliability. With standardised components and the increasing technical expertise in the industry, maintenance is predictable and less prone to failure when proper procedures are followed.
Environmental and Regulatory Advantages
1. Natural Refrigerant with Minimal Environmental Impact
CO₂ (R-744) is a natural refrigerant that is non-flammable and non-toxic (under controlled concentrations), with a Global Warming Potential (GWP) of just 1 — a stark contrast to the high-GWP values of HFCs. This makes it a strong candidate for companies committed to emissions reduction and sustainability.
2. Compliance with F-Gas and Future Legislation
While HFCs are being phased out under the F-Gas Regulation, CO₂ remains unaffected by quotas or market restrictions within the European Union. This provides long-term regulatory stability and makes CO₂ a future-proof investment.
Where is CO₂ Refrigeration Being Used?
A growing number of businesses are transitioning to CO₂ refrigeration systems, especially in sectors where efficiency and temperature stability are critical:
- Supermarket chains aiming to cut carbon emissions and reduce energy consumption.
- Meat and fish processing industries where thermal consistency is crucial in production and storage areas.
- Temperature-controlled logistics hubs requiring precise management of cold storage and freezing zones.
Thanks to its versatility, CO₂ can be implemented across a wide range of settings — from small shops to large industrial plants.
Technical Challenges and Current Solutions
1. Initial Investment
One of the main barriers is the higher upfront cost. However, when considering the return on investment from energy savings, lower maintenance requirements, and regulatory compliance, CO₂ refrigeration becomes a cost-effective option over time.
2. Need for Specialised Training
The design, installation, and servicing of transcritical CO₂ systems demand a high level of technical expertise. At Bernad®, our team is fully trained and experienced in this technology, capable of handling projects of any scale with full assurance.
We work closely with leading manufacturers and stay up to date with the latest developments, ensuring that our solutions are safe, efficient, and compliant with all relevant standards.
Is CO₂ the Future of Industrial Refrigeration?
All signs point to yes. CO₂ refrigeration is no longer an emerging technology — it is now a robust, proven, and sustainable solution. With current technological support and accumulated industry experience, this approach is not only viable but also advisable for companies looking to stay ahead of regulations and enhance operational performance.