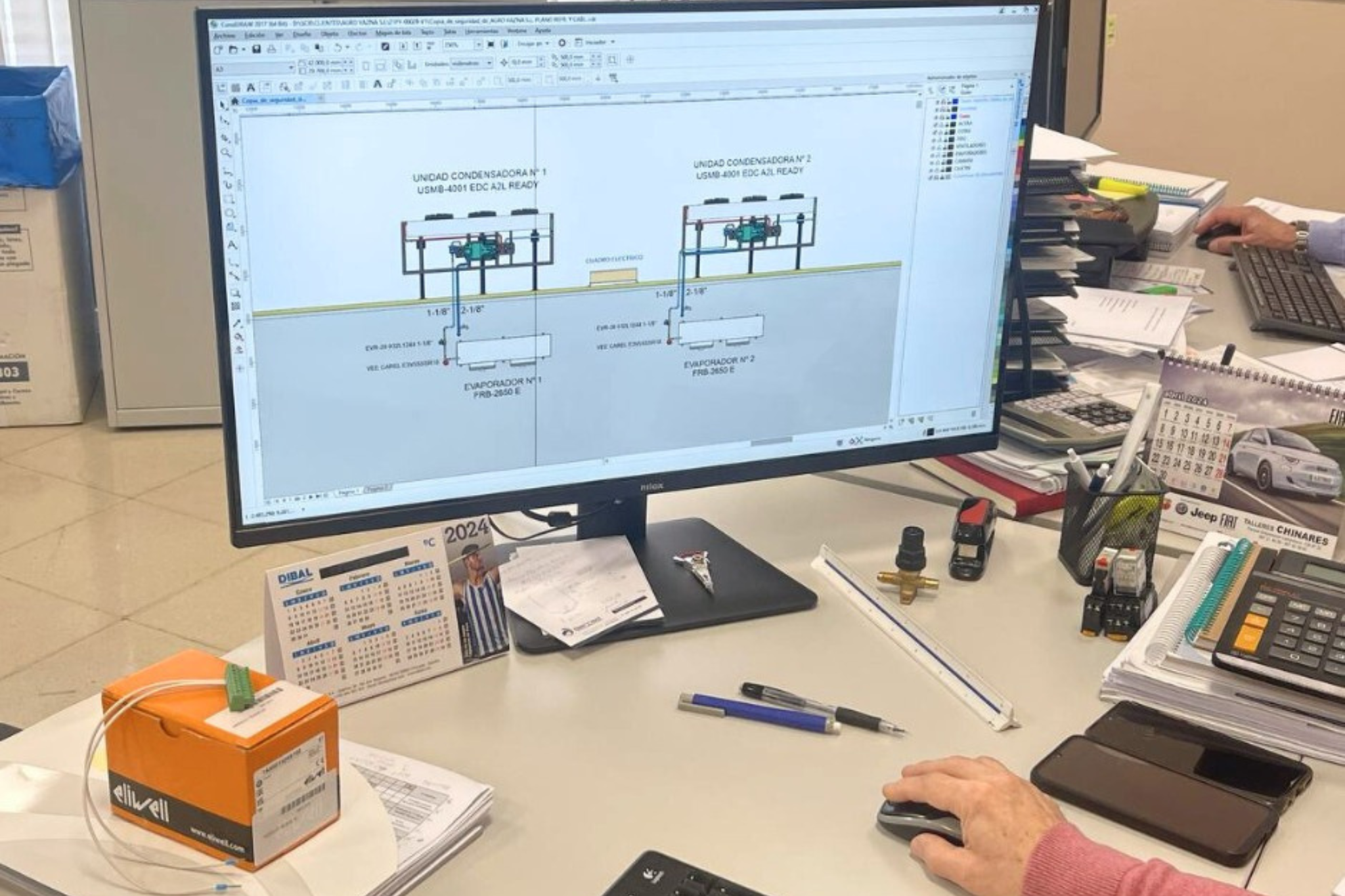
30 Jan HOW TO AVOID COMMON MISTAKES IN INDUSTRIAL REFRIGERATION SYSTEM DESIGN
Designing an efficient industrial refrigeration system is not just about selecting the best equipment; it involves making smart decisions from the outset. Mistakes at this stage can lead to high costs, operational failures, and reduced productivity. Here, we outline the most common errors and provide practical advice on how to avoid them.
1. Underestimating the Actual Thermal Load
A common mistake is miscalculating the thermal load, leading to oversized or undersized systems. This not only increases initial costs but also affects energy efficiency.
How to avoid it?
- Conduct a thorough analysis of the actual cooling requirements, considering factors such as insulation, door opening frequency, and external environmental conditions.
- Consult specialists in thermodynamics and refrigeration to ensure precise calculations.
2. Overlooking System Flexibility
In many cases, refrigeration systems are designed to meet current requirements without considering future changes. Cooling needs may evolve due to plant expansion or modifications in production processes.
How to avoid it?
- Design modular systems that can be easily expanded.
- Implement smart controls that adapt to different load levels.
3. Ignoring the Impact of Refrigerant Selection
Choosing the wrong refrigerant can have severe consequences in terms of efficiency, environmental impact, and regulatory compliance.
How to avoid it?
- Carefully evaluate the available options based on both local and international regulations.
- Select low-GWP (Global Warming Potential) refrigerants to comply with future regulations and minimise environmental impact.
4. Poor Placement of Components
Incorrect placement of condensers, evaporators, and compressors can cause performance issues. For instance, installing a condenser in an area with poor ventilation will increase the system’s working pressure.
How to avoid it?
- Conduct a detailed analysis of the available space to ensure proper airflow.
- Consider factors such as maintenance accessibility and minimising exposure to extreme temperatures.
5. Neglecting Control Systems
A system without adequate controls may operate inefficiently, increasing energy costs and reducing equipment lifespan.
How to avoid it?
- Implement automated monitoring and control systems that optimise operation based on demand.
- Ensure controls are intuitive and allow for quick adjustments.
6. Inadequate Testing and Commissioning
A critical mistake is not dedicating enough time to the testing and commissioning phase. This can leave hidden faults that only emerge during full operation.
How to avoid it?
- Conduct rigorous testing under real operating conditions.
- Invest in a training programme for personnel responsible for operating and maintaining the system.
Conclusion
The design of industrial refrigeration systems is a complex process that requires attention to every detail. Avoiding these common mistakes will not only save money in the long run but also ensure a reliable and efficient system. Remember: good design always starts with meticulous planning and expert advice.