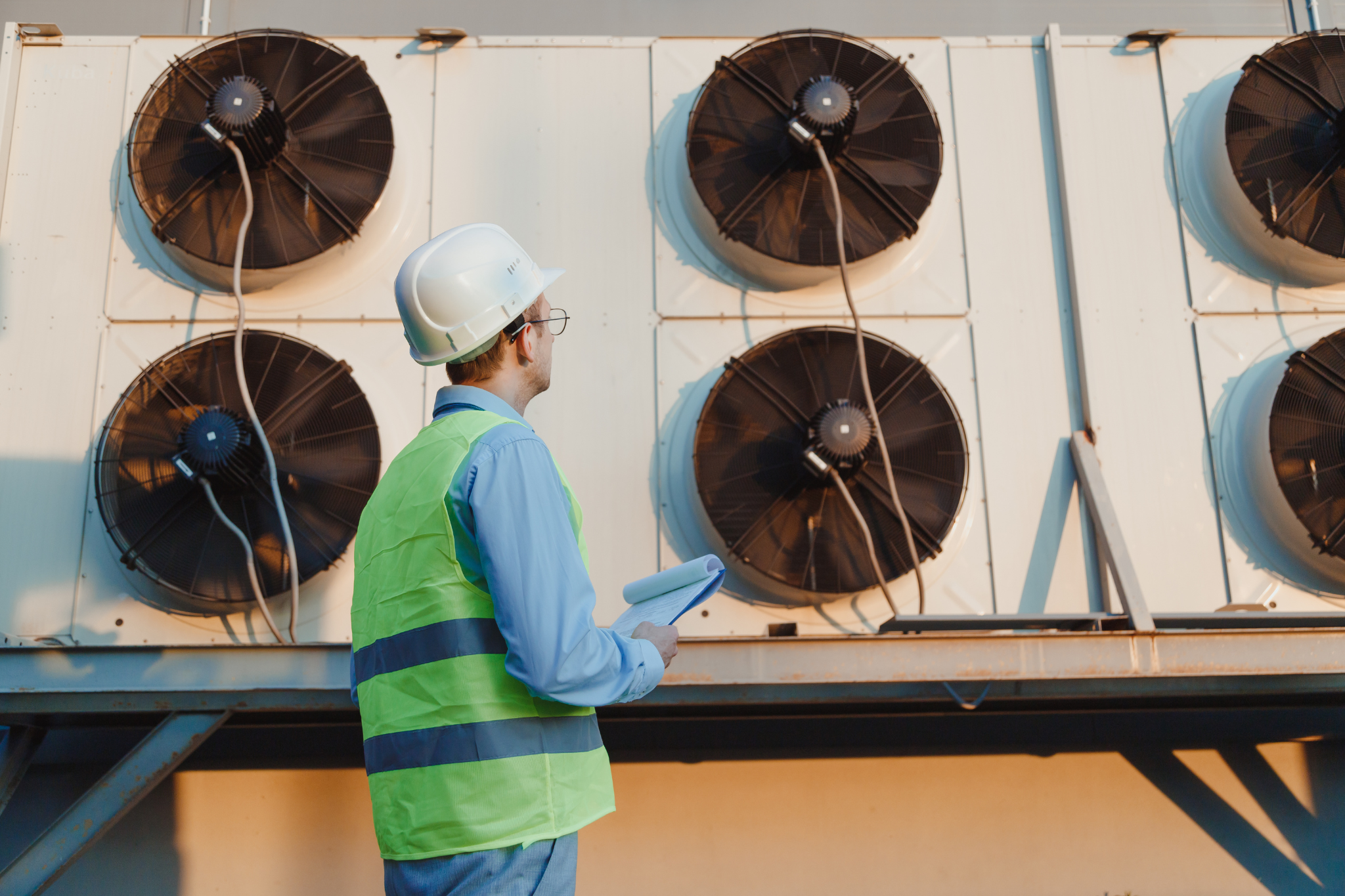
07 Mar REPLACEMENT VS. REPAIR
Replacement vs. Repair: When Is It Preferable to Upgrade a System?
Industrial refrigeration is a key component in industries such as food processing, pharmaceuticals, and logistics. The performance and efficiency of these systems directly impact business operations and profitability. However, over time, any equipment experiences wear and tear, raising a fundamental question: Is it better to repair or replace it?
Making the right decision can lead to lower operating costs, improved energy efficiency, and more reliable operations. In this article, we will examine the key factors to consider when making the best choice.
1. Cost Assessment: Which Option Is More Profitable?
One of the main factors in deciding whether to repair or replace equipment is the financial analysis. It is essential to consider not only the immediate cost of repairs but also the cumulative cost of maintenance and energy consumption.
- Repair Costs vs. Investment in New Equipment: A common industry rule suggests that if repair costs exceed 50% of the price of a new unit, replacement is the more advisable option.
- Energy Efficiency: Modern technologies are significantly more energy-efficient, reducing long-term operating costs.
- Frequency of Breakdowns: If a system requires frequent repairs, the accumulated costs and productivity losses may justify replacing it.
If a refrigeration unit consumes excessive energy and experiences frequent failures, investing in a new system may pay off within a few years due to savings in electricity and maintenance costs.
2. Equipment Lifespan and Technological Advancements
The lifespan of an industrial refrigeration system varies depending on the model and the maintenance it has received, but it generally ranges between 10 and 20 years.
Beyond the age of the equipment, it is also crucial to assess its technological obsolescence:
- Availability of Spare Parts: If replacement parts are scarce or discontinued, repair costs increase significantly.
- Regulatory Compliance: Environmental and safety regulations are constantly evolving. Older equipment may use obsolete refrigerants or fail to meet current standards.
- Integration with Modern Technologies: New systems offer remote monitoring, precise temperature control, and enhanced failure alert mechanisms.
If your system relies on fluorinated refrigerants (HFCs), be aware that their use is being restricted by regulations such as the F-Gas Regulation in Europe. Upgrading to systems that use natural or low-GWP refrigerants not only ensures compliance but also improves efficiency and reduces environmental impact.
3. Impact on Production and Operations
A malfunctioning industrial refrigeration system can affect product quality and lead to significant financial losses.
- Downtime Due to Repairs: If repairs require extended downtime, replacing the system may be a more cost-effective solution to minimise productivity disruptions.
- Impact on Product Quality: In industries such as food processing and pharmaceuticals, temperature stability is critical. A faulty system can compromise product safety and quality.
- Hidden Costs: An inconsistent refrigeration system can lead to raw material waste and complications during quality audits.
For example, if a perishable goods warehouse faces recurring refrigeration failures, losses can be substantial if temperatures are not maintained at appropriate levels.
4. Sustainability and Environmental Regulations
Sustainability is a crucial factor in modern industry. Outdated equipment tends to consume more energy and use refrigerants that are harmful to the environment.
Opting for replacement provides ecological benefits such as:
✔ Use of natural refrigerants such as CO₂ or ammonia.
✔ Reduction in greenhouse gas emissions.
✔ Compliance with evolving environmental regulations.
Additionally, government incentives and financing programmes may help facilitate the transition to more efficient and sustainable technologies.
5. Key Performance Indicators (KPIs) for Decision-Making
To determine whether to repair or replace a system, it is advisable to analyse key performance indicators such as:
- Energy efficiency (COP – Coefficient of Performance).
- Maintenance costs over the past three years.
- Mean Time Between Failures (MTBF).
- Production impact due to system failures.
If these KPIs show a downward trend, replacement is likely the best option.
Conclusion: When Is It Better to Repair and When to Replace?
The decision to repair or replace a refrigeration system should be based on a thorough analysis of costs, efficiency, and operational performance. Assessing factors such as failure frequency, energy consumption, and technological obsolescence will help determine the best course of action to optimise resources and ensure a reliable, efficient system.
If you are considering upgrading your refrigeration system, consulting with a specialist is highly recommended to select the solution that best meets your specific needs.